*On June 1, 2023 Emerson’s Climate Technologies business became a new standalone company – Copeland. Though our name has changed, we are building on more than a century of HVACR innovation and industry leadership, and Copeland continues to offer the same products, industry stewardship, and learning opportunities you’ve grown to trust. Information found on this webpage posted before June 1, 2023 may contain our old name or branding, but you can be at ease knowing it was created with the knowledge and expertise of Copeland.
When we consider the emerging class of low-global warming potential (GWP) refrigerants, the natural alternative CO2 (or R-744) already has a seat at the commercial refrigeration table. CO2 has been used successfully in global refrigeration applications for more than two decades, yet it’s still in the early stages of adoption in the U.S. But as refrigerant regulations and sustainability objectives continue to drive supermarket refrigeration decisions, CO2 transcritical booster (TCB) systems are poised to play a much larger role. As part of our Journey to Lower-GWP Refrigerants E360 Webinar series, Brent Cheshire, Copeland’s manager of end user services, and I discussed strategies for Navigating the CO2 Refrigeration Landscape and shared learnings from our firsthand experiences and research on CO2 TCB systems
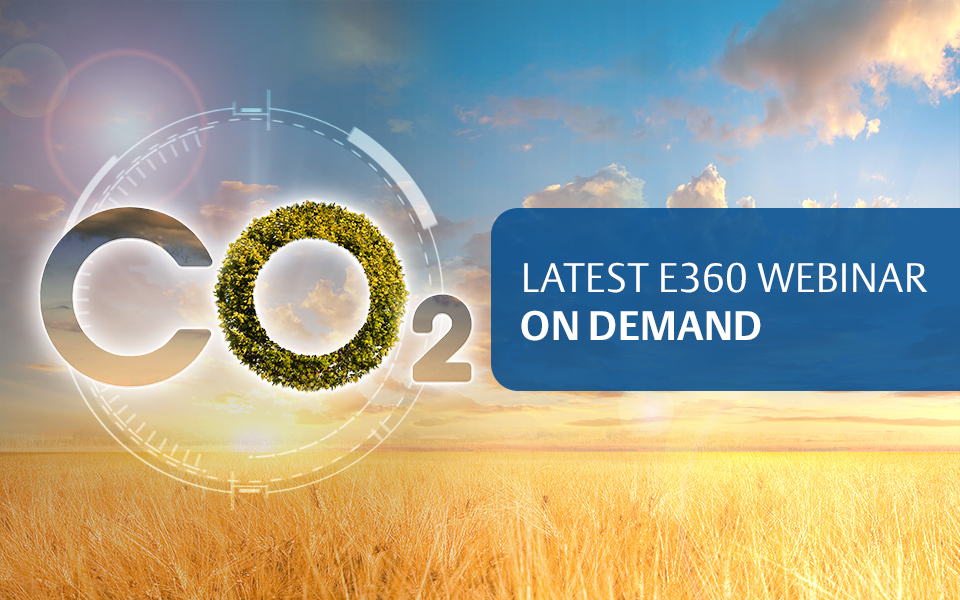
Conditions favorable for growth
To date, CO2 has found a niche primarily in large centralized systems, such as those used in supermarkets. With a GWP of 1 and zero ozone depletion potential (ODP), the A1 R-744 can be used in higher charges without introducing the same environmental concerns as legacy, high-GWP hydrofluorocarbon (HFC) refrigerants.
Current and emerging refrigerant regulations favor the use of R-744, which incidentally is already approved for use by the Environmental Protection Agency’s (EPA) Significant New Alternatives Policy (SNAP) program. Per the California Air Resources Board’s (CARB) active ruling, systems charged with more than 50 pounds must use a refrigerant with less than 150 GWP — making CO2 TCB systems a logical choice for large applications. From a federal rulemaking perspective, the American Innovation and Manufacturing (AIM) Act has mandated a 40 percent reduction in HFC production in 2024, which will further limit HFC supplies and increase demand for readily available, low-GWP alternatives, such as CO2.
Of course, many U.S. food retailers are making environmental, sustainability and governance (ESG) commitments and defining a path to Net Zero emissions. As they explore options to reduce the environmental footprint of their refrigeration portfolios, CO2 offers a viable alternative to HFCs for their large, centralized refrigeration requirements.
Refrigerant characteristics and system mechanics
Among the primary concerns about transitioning to CO2 refrigeration are the refrigerant’s unique performance characteristics and their impacts on system design and operation. As a reference point, Brent and I compared the differences between a typical HFC system and a CO2 TCB system. Having been involved in more than 250 CO2 TCB installations, Brent shared his expertise and offered many anecdotes which shed light on key aspects of system installation, baselining, start-up and commissioning. To guide our discussion, we framed the differences between HFC and CO2 systems into five focus areas:
- High operating pressures — impacts on system design and best practices for safe operation
- Lower critical point — understanding the pressure transition from subcritical to supercritical (transcritical) modes
- Higher triple point — charging considerations and the potential for a refrigerant phase change to dry ice
- Standstill pressure — importance of managing system pressures while the system is powered down and/or not operating (e.g., power outage or routine maintenance)
- Reliance on controls — recognizing the need for system, case and high-pressure controls to automate system management and regulate pressures
Brent shared that although many technicians may have apprehensions when first dealing with those unique characteristics, their concerns quickly fade once they become familiar with the basics of CO2 TCB systems. He also walked through the key steps of system baselining and start-up procedures and explained how Copeland’s E3 supervisory control provides a variety of built-in, CO2-specific functionalities to help with all aspects of system commissioning, operation and management.
High-ambient strategies and proof of concept
Another perception about CO2 TCB systems is that they’re mainly well-suited for use only in cooler climates. However, as CO2 TCB refrigeration technologies and controls have improved in recent years, system designers and original equipment manufacturers (OEMs) have introduced strategies to optimize system performance in all climates — including cold, hot, wet, dry and everything in between.
Copeland recently partnered with Future Green Now, an engineering firm with deep CO2 refrigeration expertise, to research how CO2 TCB system design optimization strategies perform in a variety of U.S. climate zones. This report, which will soon be available on request, compared the effectiveness of leading high-ambient design strategies — such as parallel compression, adiabatic gas cooling and high pressure gas ejectors — and demonstrated their relative efficiencies in these climate zones.
Today, these techniques are already being used to great success. In a recent CO2 TCB installation, Copeland supported its OEM partner, Zero Zone, to utilize an adiabatic gas cooler for a warm-weather, Southern grocery location. The system leverages Copeland’s fully integrated compression, controls, high-pressure valves and enterprise software to optimize CO2 TCB system efficiencies and deliver robust, reliable performance throughout all seasons.
To learn more about CO2 refrigeration best practices and the continued evolution of CO2 technologies, please view this webinar in its entirety. For more information, please visit Copeland’s E360 content hub for a wide variety of CO2-specific resources, including blogs, articles, videos, white papers and infographics.

Six Ways to Reduce Food Waste by Tracking the Supply Chain
*On June 1, 2023 Emerson’s Climate Technologies business became a new standalone company –...
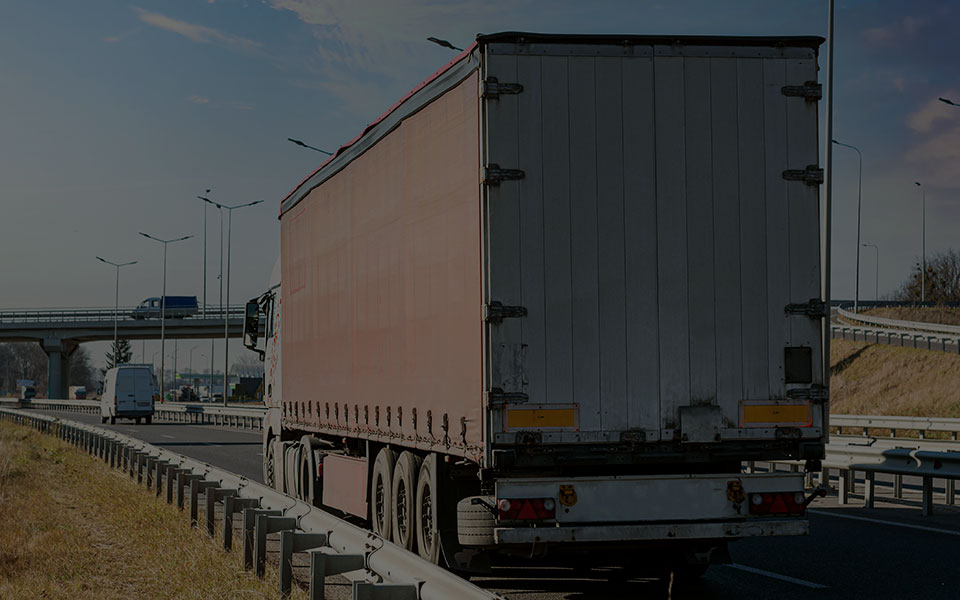
Protect Valuable Shipments in High-Crime Areas
*On June 1, 2023 Emerson’s Climate Technologies business became a new standalone company –...
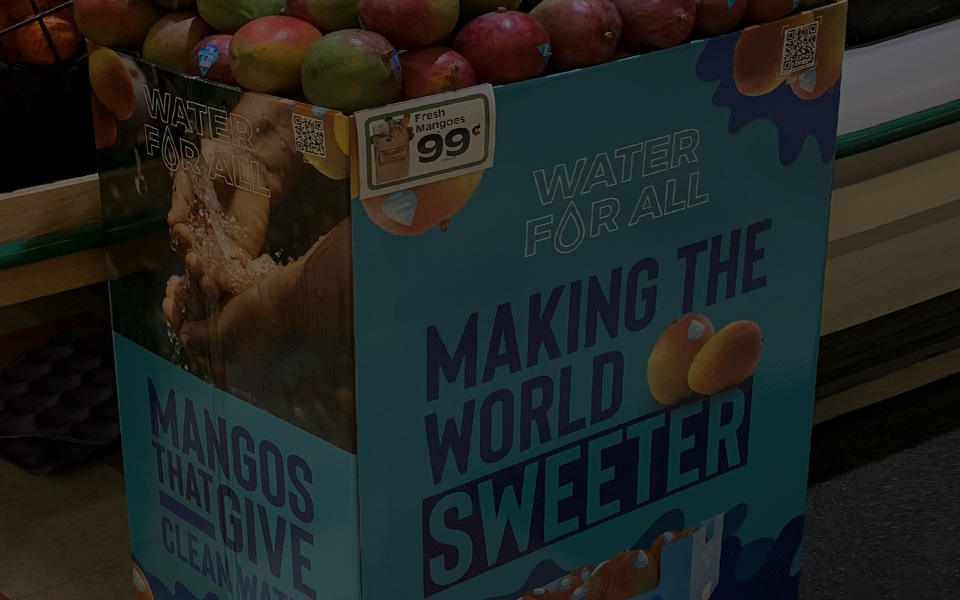
Real-time Tracking Protects Valuable Mango Cargo
*On June 1, 2023 Emerson’s Climate Technologies business became a new standalone company –...